When it comes to choosing between Aluminium 1100 and Aluminium 1200, understanding the properties and applications of these materials is crucial. Both are popular grades of aluminium with unique characteristics that make them suitable for various industrial uses. In this ultimate guide, we will compare Aluminium 1100 and 1200, discussing their key properties, differences, and best uses in industry.
What is Aluminium 1100?
Aluminium 1100 is a commercially pure aluminium alloy with a composition of approximately 99% aluminium. Known for its excellent corrosion resistance, high thermal and electrical conductivity, and ease of fabrication, Aluminium 1100 is widely used in applications where moderate strength is required.
- Aluminium 1100 H14 is a common temper designation that refers to the material’s condition. The H14 temper means it is strain-hardened to a medium level, providing a balance of strength and formability.
- Aluminium 1100 Properties: This grade is known for its ductility, excellent workability, and resistance to corrosion. However, it has lower strength compared to other aluminium alloys like Aluminium 6061 or Aluminium 2024.
What is Aluminium 1200?
Aluminium 1200, also known as Aluminum Alloy 1200, is another commercially pure aluminium alloy that shares many similarities with Aluminium 1100. However, Aluminium 1200 contains a slightly different composition, which affects its properties.
- Aluminium 1200 Properties: It offers similar corrosion resistance and workability to Aluminium 1100, but Aluminium 1200 has slightly higher strength, making it suitable for more demanding applications.
- Alloy Composition: While Aluminium 1200 is also close to 99% pure, the added elements may vary slightly depending on the specific alloy designation, contributing to higher strength.
Key Differences Between Aluminium 1100 and Aluminium 1200
Let’s break down the key differences between Aluminium 1100 and 1200:
Property | Aluminium 1100 | Aluminium 1200 |
---|---|---|
Purity | 99% Pure | 99% Pure |
Strength | Low | Slightly Higher |
Corrosion Resistance | Excellent | Excellent |
Workability | Excellent | Excellent |
Applications | Decorative, Electrical | Heavy-duty industrial |
Aluminium 1100 H14 vs Aluminium 1200
Both Aluminium 1100 H14 and Aluminium 1200 offer excellent corrosion resistance and workability, but Aluminium 1100 H14 is a strain-hardened version that provides more strength compared to the annealed version of Aluminium 1100. This makes it suitable for applications requiring a balance between formability and strength, such as electrical components and decorative finishes.
- Al 1100 Properties: When in the H14 temper, Aluminium 1100 has increased strength due to strain hardening, yet it still retains its ductility and excellent corrosion resistance.
- Aluminium 1200: The slight increase in strength makes Aluminium 1200 more appropriate for industrial applications requiring more durability.
Applications of Aluminium 1100
Because of its excellent corrosion resistance, formability, and electrical conductivity, Aluminium 1100 is ideal for:
- Electrical Conductors: Aluminium 1100 is commonly used in electrical applications, such as cables and wiring, due to its high electrical conductivity.
- Chemical and Food Processing: Aluminium 1100’s excellent resistance to corrosion makes it ideal for tanks, pipes, and other equipment used in chemical and food processing industries.
- Decorative Finishes: It is widely used for decorative items due to its aesthetic appeal and ease of fabrication.
Applications of Aluminium 1200
While Aluminium 1200 shares many characteristics with Aluminium 1100, it is better suited for:
- Heavy-Duty Industrial Applications: Aluminium 1200 is used in applications that require more strength, such as industrial machinery parts, heavy-duty frames, and structural components.
- Marine Environments: Due to its excellent corrosion resistance and slightly higher strength, Aluminium 1200 is a preferred material in marine environments where exposure to saltwater is common.
Aluminium Alloy 1100 Properties and Uses
As we’ve mentioned earlier, Aluminium Alloy 1100 offers exceptional corrosion resistance, making it ideal for applications in areas with high humidity or exposure to corrosive elements. This alloy is not typically used in structural or load-bearing applications, as its strength is relatively low compared to other alloys. However, it is widely used in the production of:
- Architectural Materials: Aluminium 1100 is commonly used in roofing, siding, and gutter systems.
- Heat Exchangers: Due to its excellent thermal conductivity, it is used in heat exchangers, cooling systems, and radiators.
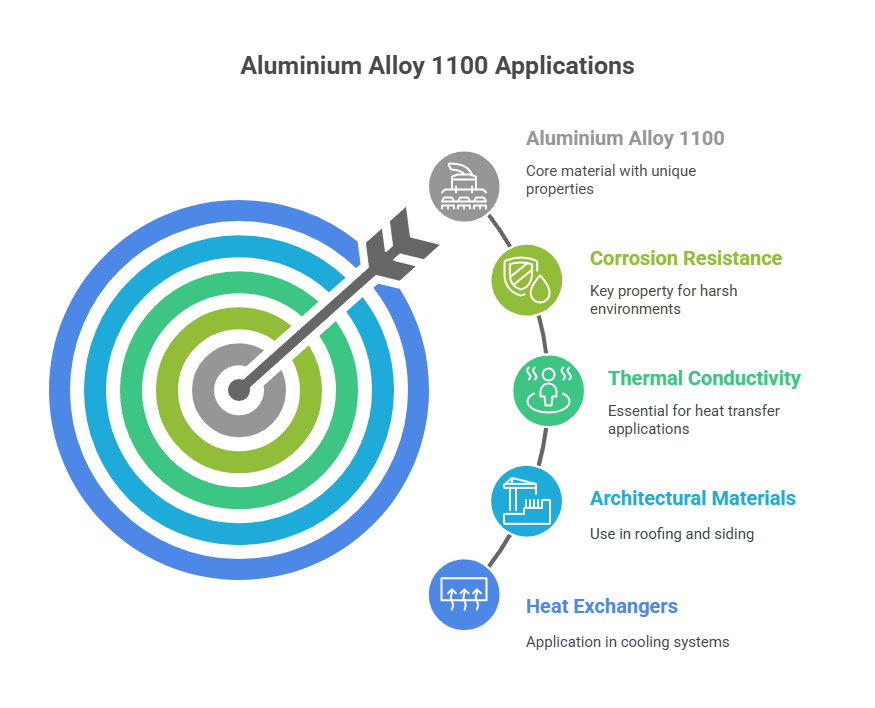
Conclusion
Both Aluminium 1100 and Aluminium 1200 offer excellent corrosion resistance and workability, but they differ in strength and suitability for various applications. Aluminium 1100, particularly in the H14 temper, is ideal for applications that require high electrical conductivity and corrosion resistance, while Aluminium 1200 provides higher strength, making it more suitable for heavy-duty industrial applications. Understanding the differences between these two alloys will help you select the best material for your project.
FAQs
ST52 is primarily used in structural applications such as beams, columns, and chassis in the construction and automotive industries. It’s also used in machinery for parts requiring high strength and durability.
The ST52 material composition includes 0.22% carbon, 1.60% manganese, and small amounts of silicon, sulfur, and phosphorus. This combination ensures the material’s strength and toughness.
ST52 has a yield strength of around 355 MPa, making it ideal for heavy-duty applications that require high load-bearing capacity.
ST52 is similar to S355J2 in terms of mechanical properties, particularly in terms of yield strength. However, ST52 offers slightly better weldability and is preferred for certain structural applications.
The ST52 material equivalent includes S355J2 in the European standard, A572 Grade 50 in the U.S., and SS400 in Japan, offering similar mechanical properties for international use.